The Monolithic Dome
The Monolithic Dome is a thin shell structure used worldwide for homes, schools, safe rooms, gymnasiums, bulk storages, churches and more. It is constructed with polyurethane foam, steel rebar and concrete. Together, these materials create a disaster-resistant, energy-efficient and free-span structure. The cost of using these high-quality construction products is made affordable because of the dome shape’s efficient use of materials. A dome covers more area with fewer materials than any other comparable structure.
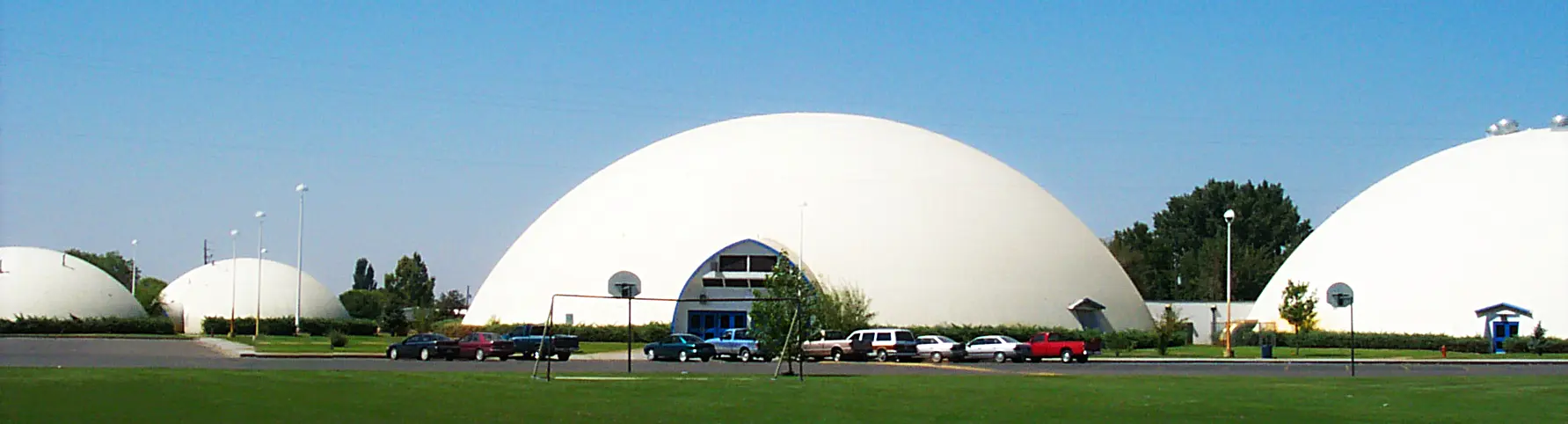
Built by Monolithic in 1986, Emmett High School in Emmett, Idaho was the first Monolithic Dome school ever built. The domes provide the campus with 110,000 square feet of classrooms and shops.
There are thousands of Monolithic Domes throughout the United States and the world — from the Arctic to the tropics. They are used for schools, storages, churches, homes, gymnasiums, safe rooms and more. There are domes as small as 8-feet to over 340-foot in diameter with engineering for even larger structures.
They have withstood major earthquakes, powerful tornadoes, raging fires, direct hits by hurricanes, and fiery explosions. Monolithic Dome owners report energy savings greater than 50 percent over conventional structures. There are no columns or interior supports, allowing complete design freedom. And the most surprising feature is the Monolithic Dome’s affordability. Economies of scale at play often make the Monolithic Dome less expensive to construct than traditional structures.
Benefits
Energy savings
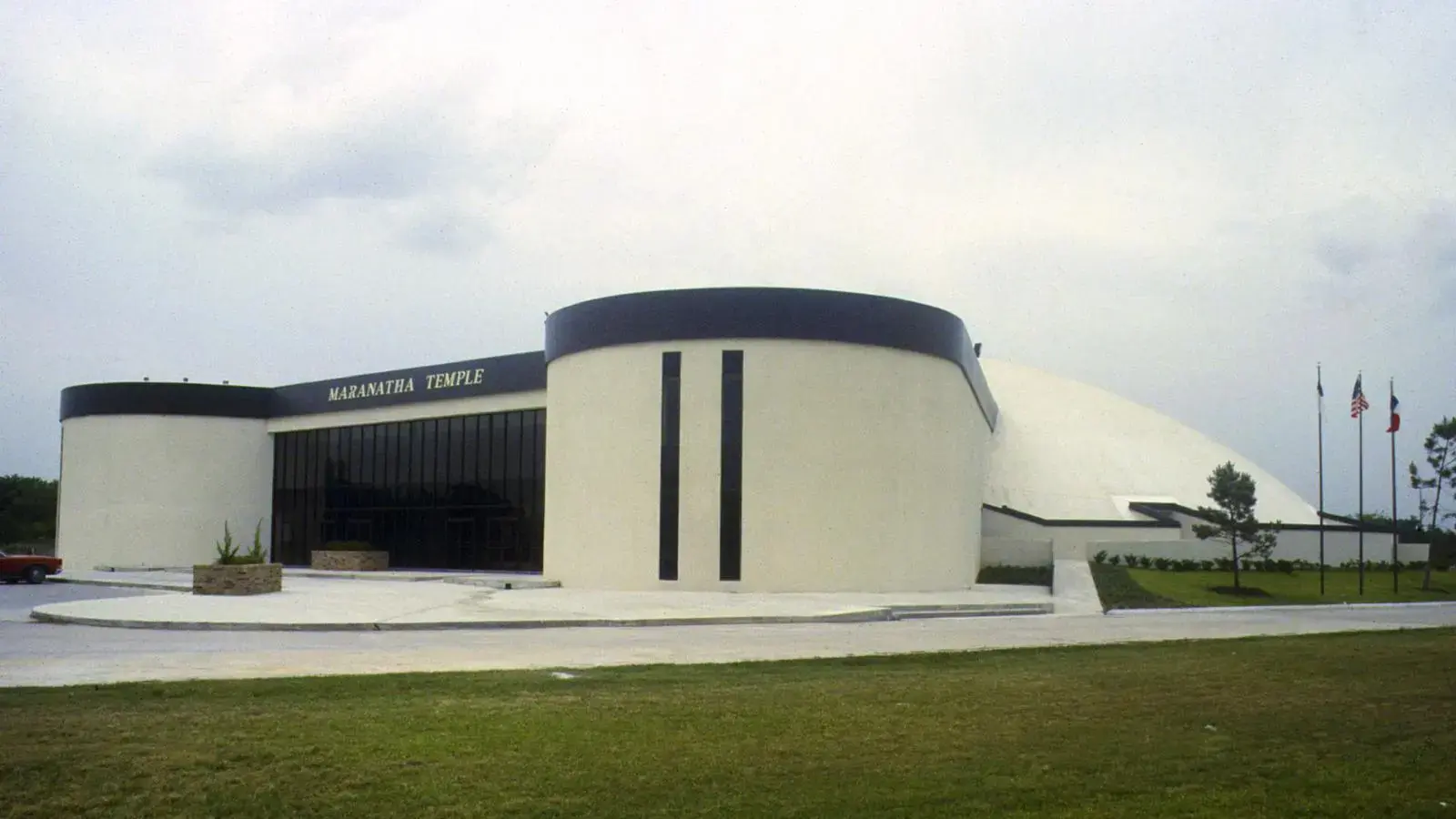
The energy savings documented by the pastor of the Maranatha Christian Center (built by Monolithic in 1984) were $60,000 per year in the 1990s. These funds, had they been invested at 7 percent per annum, would have paid for the structure in less than 14 years.
Energy savings are realized because of the unique way concrete and foam work together in the Monolithic Dome to create a passive solar structure. Most conventional buildings are insulated on the inside of the buildings. The Monolithic Dome has a layer of polyurethane foam covering the building’s structural concrete on the outside. This enables the dome’s concrete to act as a thermal battery.
In layman’s terms, this means, in cold weather, you warm up the interior of the dome and the concrete absorbs and stores the heat—while the polyurethane keeps that heat from being radiated outside. The heat stored in the concrete radiates throughout the structure, minimizing temperature fluctuations and ultimately saving Monolithic Dome owners money in Energy costs. The same holds in hot climates. The concrete is cooled down inside, the polyurethane protects it from the hot temperatures outside, and any heat generated inside (from people in the house or cooking, etc.) is then absorbed by the concrete—keeping the interior cool.
Here is a list of articles on Monolithic.org about energy savings.
Disaster resistance
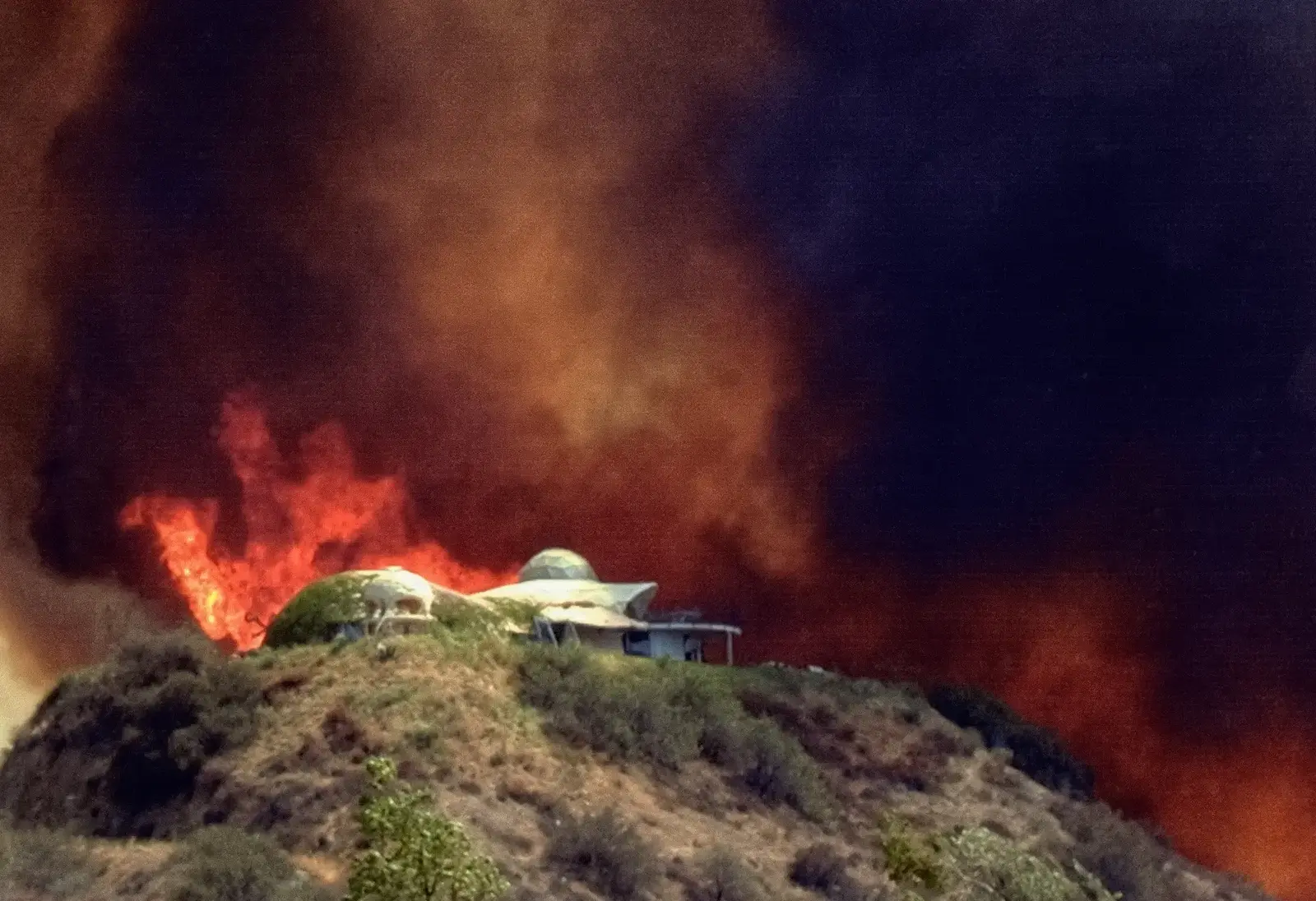
August 11, 2002, The Bryant Fire swept through Yucaipa, California, and ran right over the top of Al and Ruth Braswell’s Monolithic Dome Home. When Al and Ruth evacuated, Ruth left the doors open for the fire crews, just in case. They later told her that after they saw how fireproof the dome was, they indeed had planned to use the home for shelter if they got into trouble. The fire chief told Ruth that if her home had been a conventional structure it would have burned to the ground.
The Monolithic Dome can withstand tornadoes, earthquakes, hurricanes and fire. In 2011, leading thin-shell engineer Arnold Wilson wrote,
The Monolithic Dome, because of its very nature, heads the list for economy and strength to resist extreme loads.
FEMA agrees with his assertion, and now dozens of communities have received grant money to help pay for their disaster shelters and safe rooms that double as schools, sports facilities and community centers.
We have gathered many first-hand accounts of domes that have withstood everything nature could throw at them. A few of these accounts include:
- Letter: Margaret tells her story of riding out Hurricane Michael in a Monolithic Dome home
- Animals—and people—sheltered in dome during Hurricane Michael
- The West Texas Explosion: An Avoidable Tragedy
- Hurricane Keith huffed and puffed and …
- DuPont’s Monolithic Dome Hurricane Shelter
- Foam: Fire Hazard and Fire Barrier
- Monolithic Dome Survives Texas Wildfire
- Monolithic Dome saves man from fire
- Monolithic Dome Home Survives Missouri Tornado
- Tornado Hits Monolithic Dome in Durant, Mississippi
Freedom of design
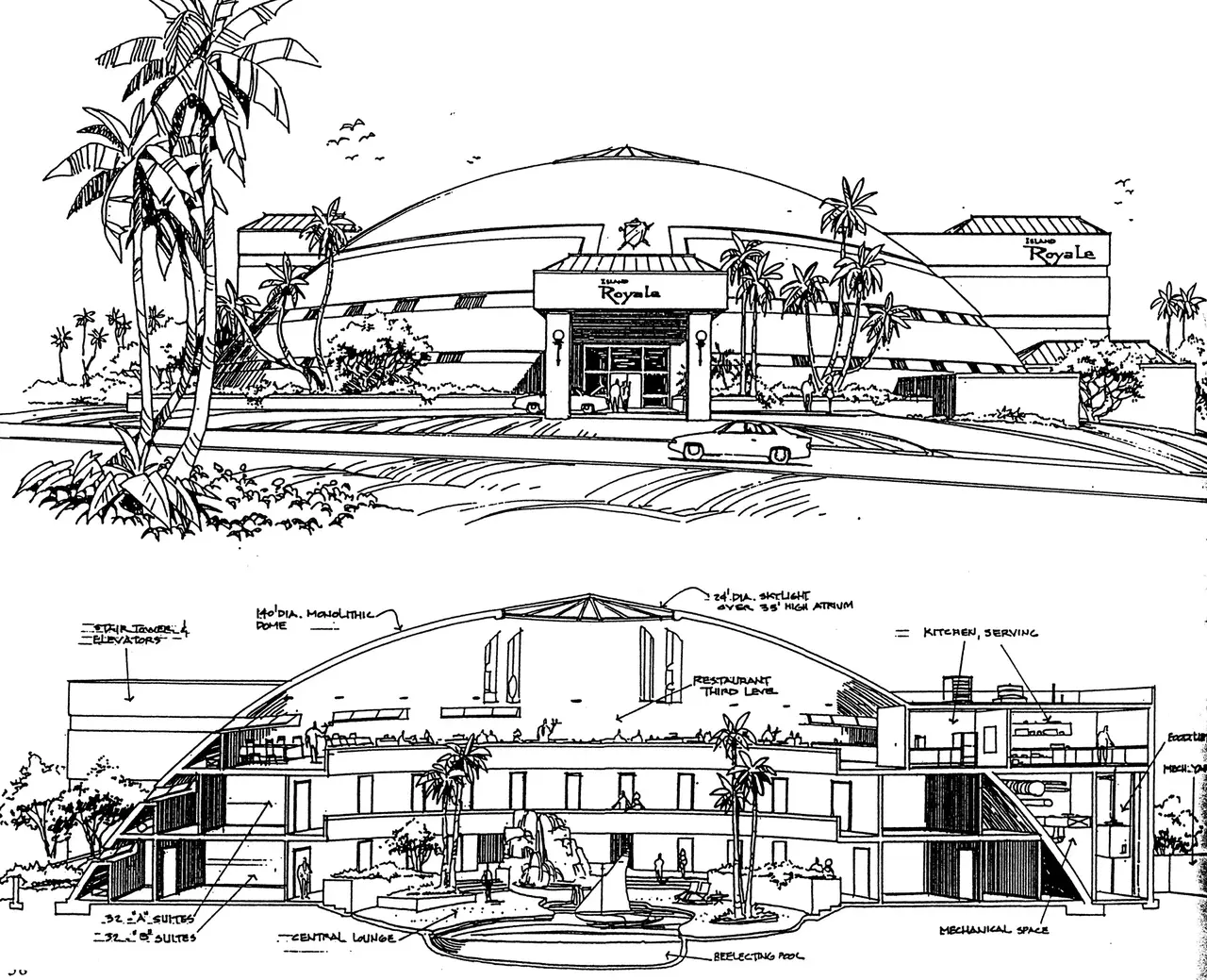
Anything you can dream up can be built inside a Monolithic Dome. This concept sketch of a multi-story hotel is one of many exciting design ideas created by architect Rick Crandall. The free span nature of the Monolithic Dome allows for total freedom of design.
Rick Crandall
The free span nature of the Monolithic Dome make it the ideal structure for freedom of design. Literally, anything under the sun can be built inside. Refer to our catalog of Monolithic Dome house plans to get an idea of how many ways domes can be constructed as residences. The open interior of the Monolithic Dome can just as easily accommodate an indoor theme park as it can be used for a home, bulk storage or a concert hall.
In addition, the ability for the Monolithic Dome Shell to support interior structures is a significant design benefit of the Monolithic Dome—both for residential and commercial applications. Examples include: second floors, balconies, staircases, mezzanines, walkways, press boxes, galleries, scoreboards, audio and video housing, and more. All of these can be anchored to and hung directly from the Monolithic Dome, reducing the costs of construction.
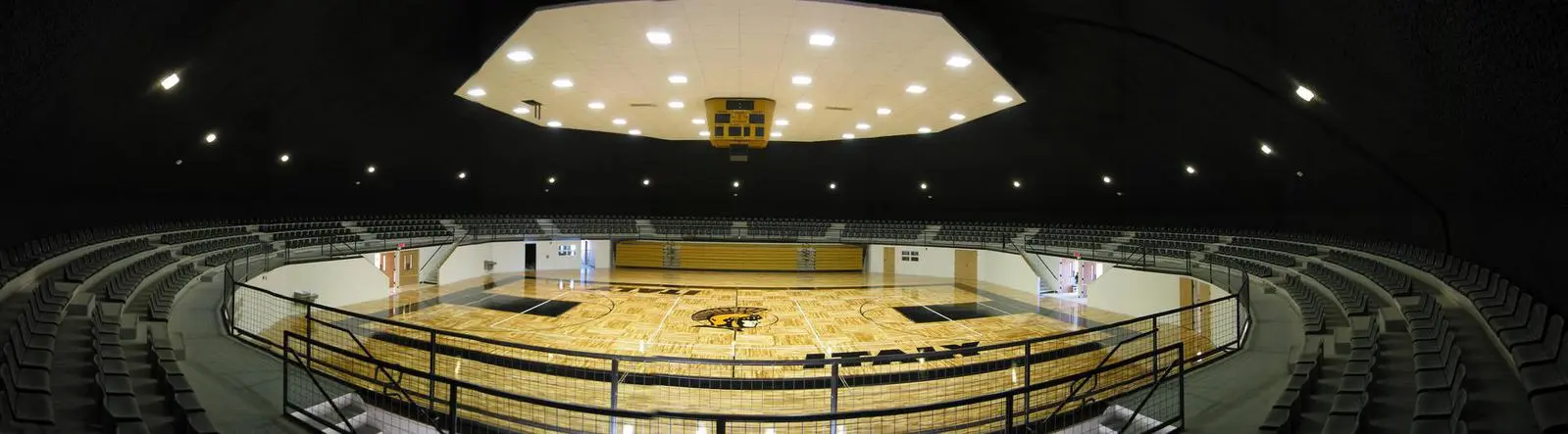
The scoreboard, sound baffling and lights were all hung directly from the Italy High School Multipurpose Center dome with no additional support or engineering required to carry the load. Built in 2002, Monolithic provided the construction management services for this project in our hometown of Italy, Texas.
Dave South
Economies of scale
To build a Monolithic Dome house, it will cost the owner about the same as it would to build a similar-sized conventional structure. This is because the materials used in the construction of a Monolithic Dome are expensive, high-quality building materials, but the shape of the building allows for efficient use of these more costly components.
However, as the size of the dome goes up, so do the savings in construction. Monolithic Domes built for schools, sports facilities, community safe rooms, storages and more will find that construction costs will often be significantly lower. When you tie in the energy savings of the Monolithic Dome, we often see buildings which pay for themselves within 20 years.
To understand how this is all possible, we need to know how to build a Monolithic Dome.
Construction Process
Monolithic Domes come in many shapes and sizes — multiple domes welded together, large domes on tall stem walls, small one-bedroom houses, and giant auditoriums. All these share the same basic construction process initially patented by the South brothers.
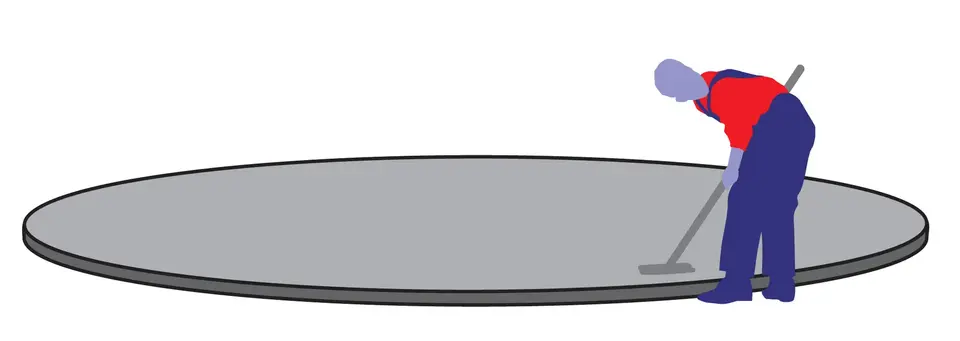
Step 1 — Ring Beam
The first step is to create a ring beam of concrete and steel. It can be a simple, circular foundation, a slab on grade floor with an integrated ring, or a tall stem wall with the ring beam seamlessly integrated near the top. Vertical steel reinforcing bars, or rebar, are embedded in the ring beam to be attached later to the steel reinforcing of the dome itself.
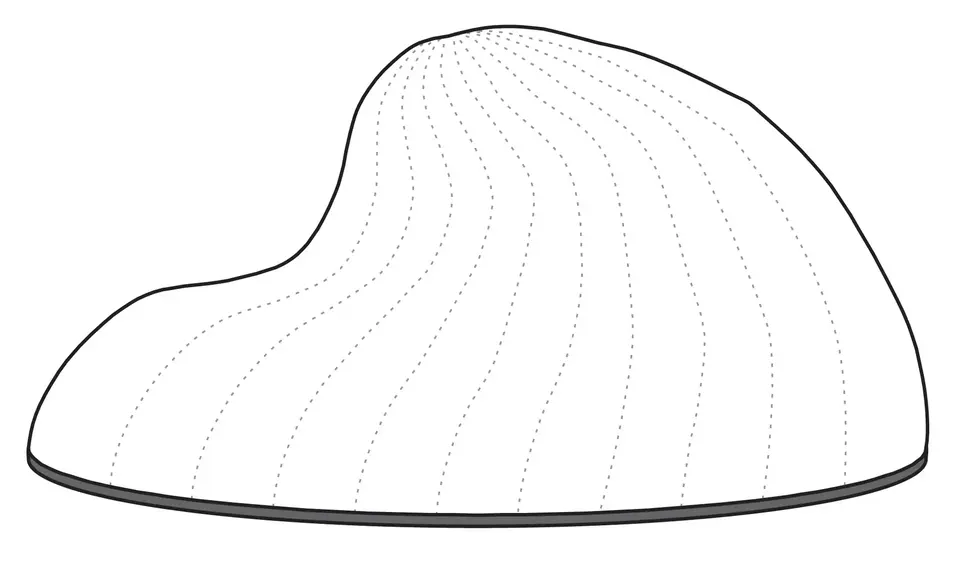
Step 2 — Airform Membrane
An airform — a tough, PVC coated fabric membrane — is manufactured to the proper size and shape. It is attached to the ring beam. Blower fans inflate the airform to create the shape of the structure to be completed. Fans run throughout construction. The airform membrane becomes the roofing membrane when the dome is finished.
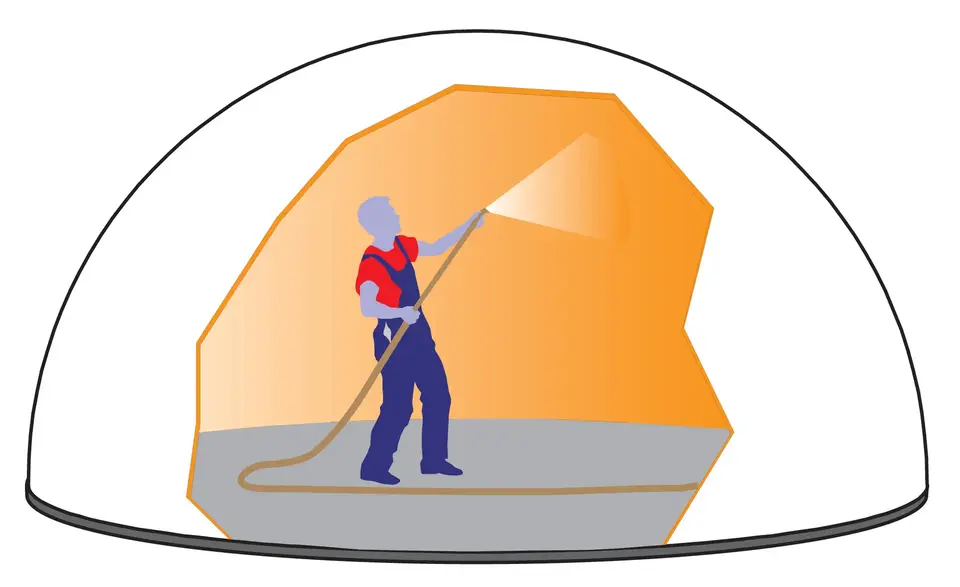
Step 3 — Polyurethane Foam
Closed-cell polyurethane foam is applied to the interior surface of the airform. Entrance into the air structure is made through a double door airlock which helps maintain a constant interior air pressure. Foam is applied in layers with “rebar hangers” embedded in the foam. Typically the foam is around three inches thick but can vary depending on the application.
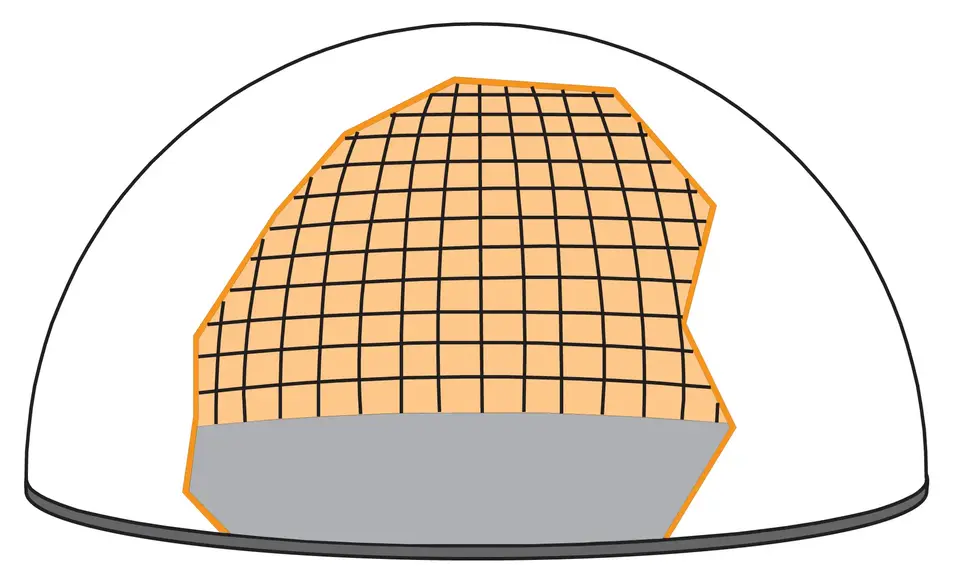
Step 4 — Steel Reinforcing
Steel reinforcing rebar is attached to the interior, foamed surface via the embedded rebar hangers. The rebar is laid out in an engineered pattern of hoop (horizontal) and vertical steel bars. Small domes need small diameter bars with wide spacing. Large domes require larger bars with closer spacing. Double mats of rebar are often used for large, load-bearing storages.
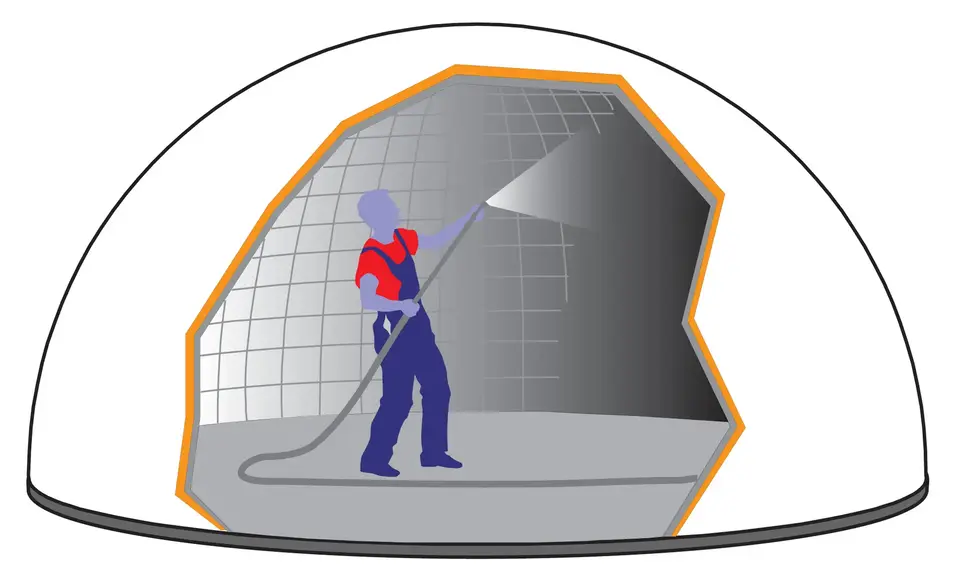
Step V: Shotcrete
Shotcrete is a unique, sprayable mix of concrete. It is applied to the interior surface of the Monolithic Dome — yes, it’s sprayed overhead in layers and not poured over the form. Small domes typically require three inches of shotcrete. More extensive dome requirements vary depending on the size and loads, but ultimately a Monolithic Dome is a thin-shell concrete structure and the amounts are remarkably efficient. The blower fans are shut off after the concrete is set and the Monolithic Dome is complete.
Finished structure
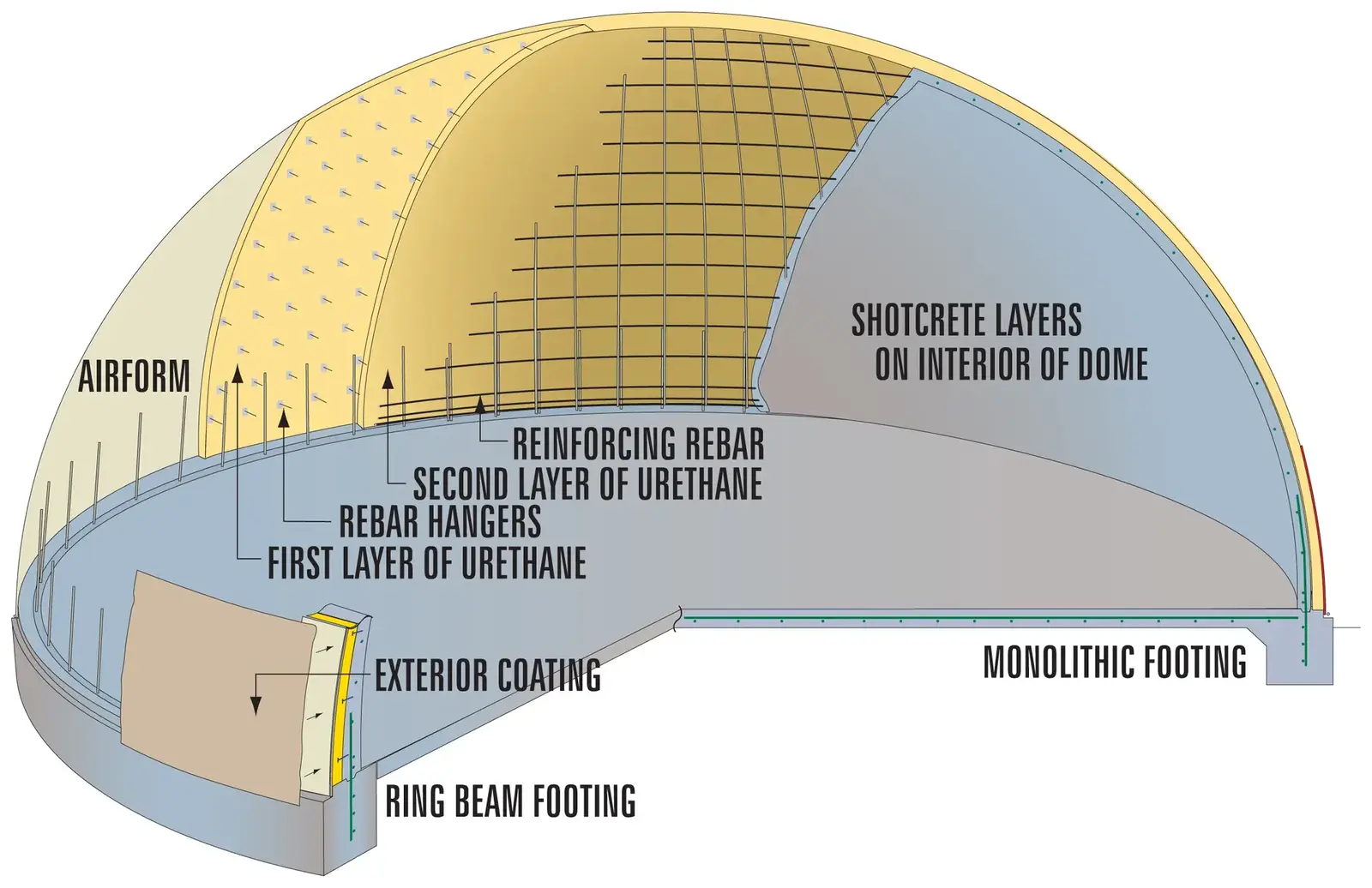
From the outside in — Monolithic Domes start as an inflated fabric form that stays on the outside of the building and acts as a single-ply roof membrane. Polyurethane foam is sprayed on the inside. Rebar is hung in a pre-engineered pattern, and a layer of shotcrete is sprayed — embedding the rebar. The result is a beautiful, affordable, disaster-resistant and energy-efficient superstructure.
The airform, foam, steel, and concrete layers form a one-piece — monolithic — thin-shell concrete dome. The airform is the roofing membrane, the foam is the insulation, the steel is the backbone and the concrete is both a thermal battery and the structure. The Monolithic Dome is the most energy-efficient, disaster-resistant, affordable building available today.